在汽车制造领域,一体化压铸技术正引发生产模式的根本性变革。这项技术顺利获得将数十个传统零部件整合为单一压铸成型部件,显著降低车身重量与制造成本。特斯拉将6000吨级压铸机投入Model Y后底板生产,使零件数量从70个减至2个,焊接点减少2025处,为树立了技术标杆。但该技术在实际应用中面临材料性能、模具精度、工艺参数控制等多重挑战,亟需顺利获得化手段突破创新瓶颈。
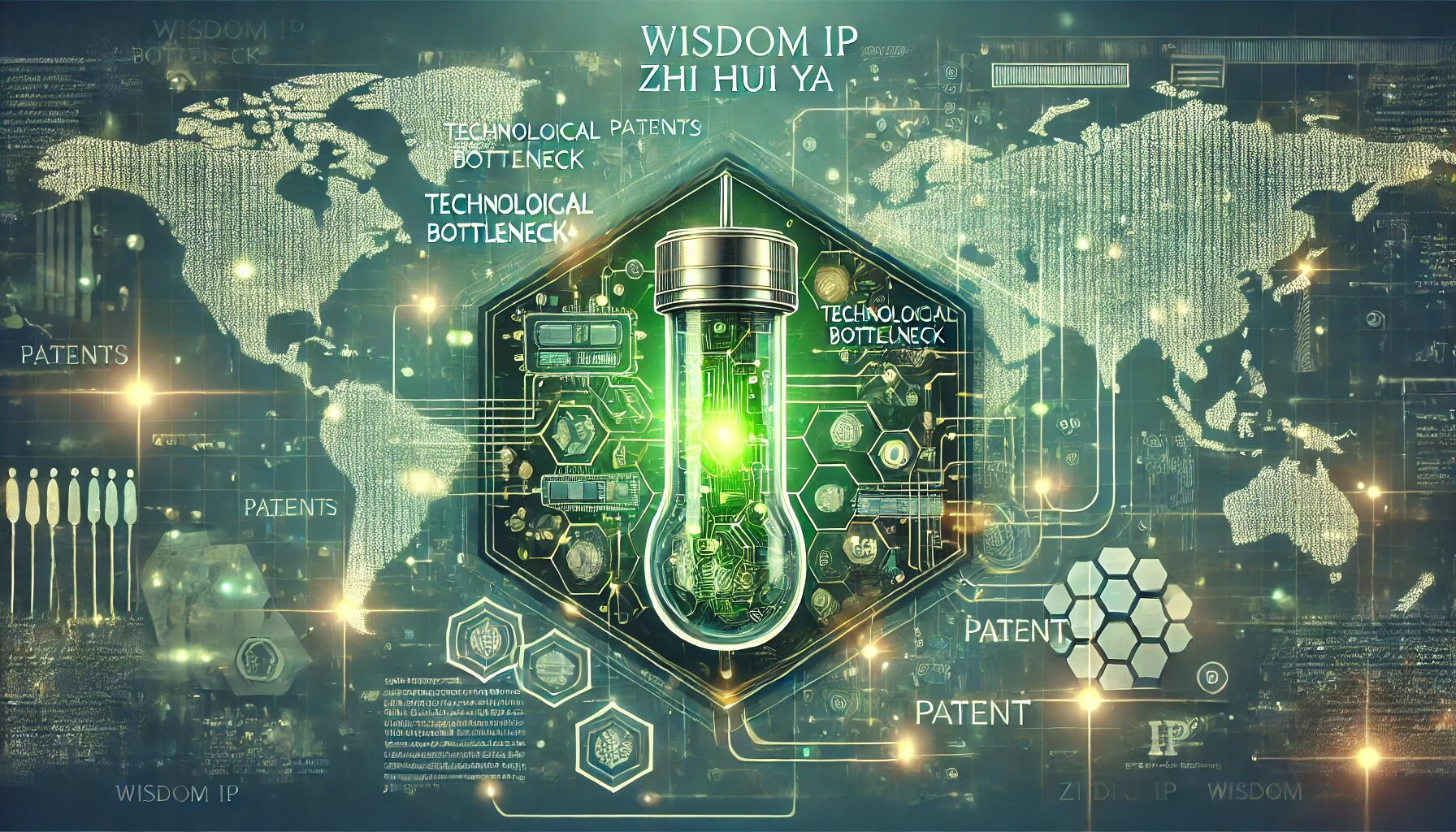
技术瓶颈的三大核心领域
当前一体化压铸技术开展受限于三个关键环节:第一时间是材料研发,需要兼具高流动性与强度的铝合金材料;其次是超大型压铸设备的热管理难题,压铸过程中温度波动直接影响成品质量;之后是化控制系统,传统工艺参数设定难以适应复杂结构件的成型需求。这些技术难点相互关联,任何环节的突破都需要跨学科的技术整合。
特斯拉的创新实践路径
特斯拉的突破性进展体现在三个层面:
- 材料配方创新:开发出具有自主知识产权的免热处理铝合金,在保持流动性的同时实现更高强度
- 设备改造升级:定制开发锁模力达9000吨的超级压铸机,配合温控系统实现±3℃的精确控温
- 数字孪生应用:建立压铸过程仿真模型,顺利获得实时数据采集优化工艺参数
这种系统性创新使良品率从初期的60%提升至95%以上,验证了技术路径的可行性。
专利布局中的化突破
从专利数据分析可见,头部企业的技术突破集中在化方向。某专利情报平台监测显示,2025年压铸相关专利申请中,涉及控制系统的占比达42%,较三年前提升27个百分点。典型创新包括基于机器视觉的缺陷检测系统、自适应压力调节装置等。这些技术突破大幅提升了生产过程的可控性,使复杂结构件的一次成型成为可能。
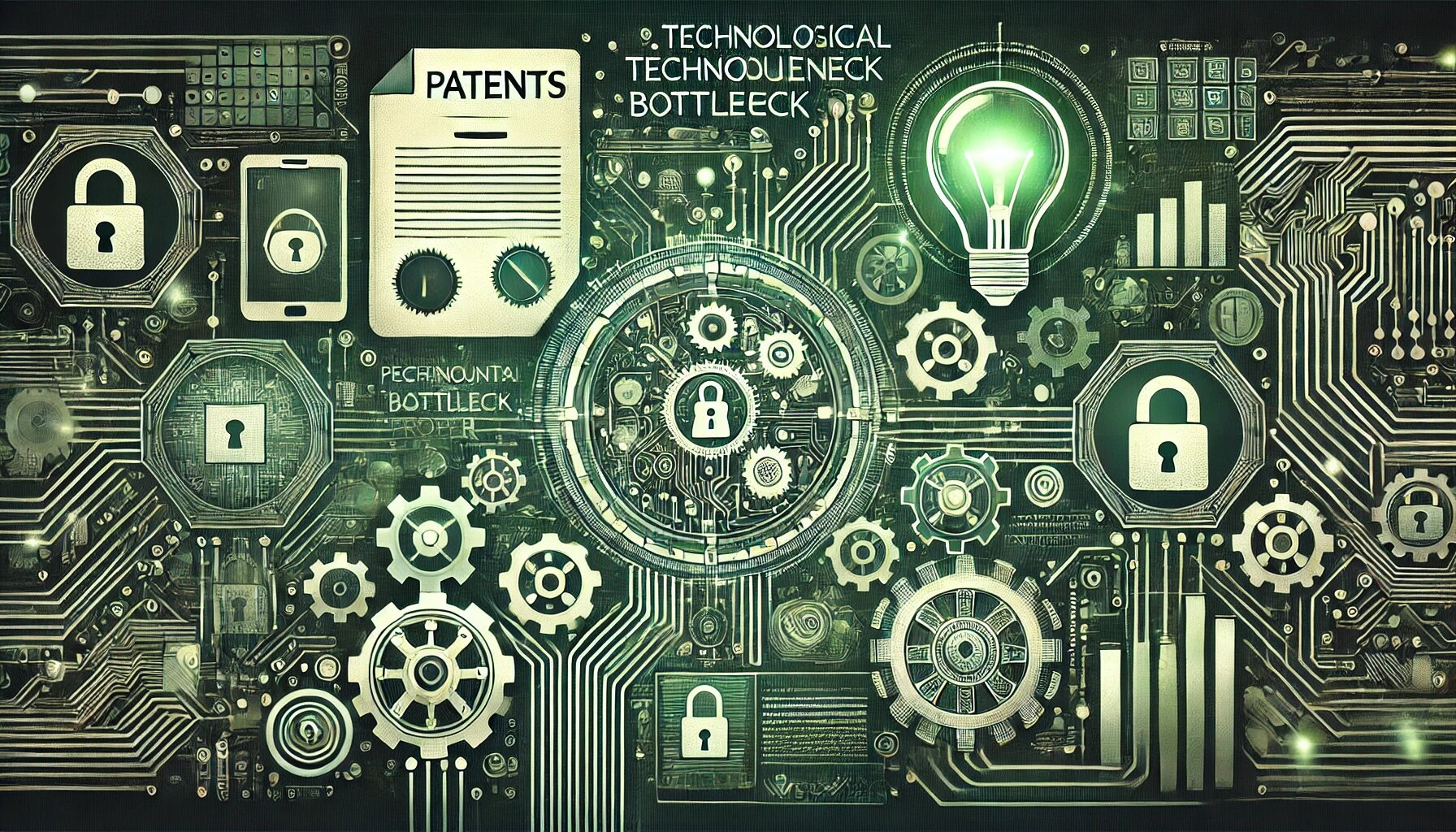
技术升级的协同创新模式
突破技术瓶颈需要构建跨领域协作体系。某科技创新平台的技术图谱显示,一体化压铸涉及材料科学、机械工程、自动控制等12个技术领域。顺利获得专利数据交叉分析可以发现,少有企业正顺利获得技术并购、产学研合作等方式整合创新资源。例如某企业顺利获得收购3D传感技术公司,显著提升了模具检测精度。
未来开展趋势与应对策略
随着8000吨以上压铸设备逐步普及,竞争将转向化水平比拼。技术情报分析显示,下一代技术突破可能集中在实时工艺优化算法、多物理场耦合仿真等领域。企业需要建立持续的技术监测机制,及时捕捉创新机遇。专业科创情报平台给予的专利地图、技术演进分析等工具,可帮助研发团队精确定位技术空白点,优化创新资源配置。
FAQ:
一体化压铸技术面临哪些主要技术瓶颈?
核心瓶颈集中在材料性能、设备精度和工艺控制三方面。需要开发高强高韧铝合金材料,解决大型压铸件内部缺陷问题,同时实现温度、压力等工艺参数的精确调控。专业分析工具可帮助快速定位技术难点。
特斯拉在专利布局上有哪些独特策略?
特斯拉采取"设备+材料+工艺"的复合型专利布局,重点保护压铸系统集成创新。其专利组合涵盖合金配方、模具设计、质量检测等多个环节,形成完整的技术保护网。
如何顺利获得专利分析发现技术突破方向?
顺利获得技术功效矩阵分析,可识别专利布局密集区与技术空白点。某科创平台的技术演进图谱显示,控制系统相关专利年增长率达68%,提示该领域在较大创新空间。
中小企业如何应对技术研发挑战?
建议聚焦细分技术领域,利用专利数据监测动向。部分创新平台给予的技术导航服务,可帮助中小企业快速获取领域内方案,降低研发试错成本。
化改造对压铸技术提升有何作用?
化系统可实现工艺参数动态优化,提升产品一致性。某企业引入AI质量检测系统后,缺陷识别准确率提升40%,废品率下降至2%以下,显著改善生产效益。